What do amusement park rides, factory assembly lines, sawmills, food processing plants, and robotic work cells all have in common? They all rely on Programmable Logic Controllers (PLCs) for automation and control.
PLCs are specialized industrial computers designed to monitor inputs, execute programmed logic, and control output devices in real-time. Their reliability, flexibility, and efficiency make them essential in modern automation, allowing for precise process control across industries. As a Rockwell Automation Gold System Integrator Solutions Partner, Concept Systems has extensive experience in designing, implementing, and upgrading PLC control systems. Let’s dive into the fundamentals of PLCs, focusing on Rockwell Automation’s industry-leading solutions.
How Does a PLC Work?
PLCs come in various models and configurations, each designed to meet specific automation needs. While different manufacturers offer unique functionalities, the core operation of a PLC remains the same: continuously monitoring inputs, executing logic, and controlling outputs.
In the United States, Allen-Bradley PLCs from Rockwell Automation dominate the market. For large-scale control applications, the ControlLogix PLC stands out, offering world-class process, safety, and motion control capabilities.
- A PLC is a task-driven control system with four basic operational steps for every device. They operate in a continuous loop to execute their control programs. The cycle consists of these 4 basic steps:
- Input Processing: Identifies the status of all input devices that are connected to the PLC.
Program Execution: Implements the user-created PLC Programming. - Output Processing: Energizes or de-energizes all connected output devices.
- Housekeeping: Communicates with programming terminals and internal diagnostics.
The order, complexity, and timing of these steps depend on the model and manufacturer of PLC being used and how the PLC programming is setup. For detailed information from Rockwell Automation on Tasks and scans see: Logix 5000 Controllers Tasks, Programs, and Routines
What are input/output (I/O) devices?
Input and output (I/O) devices are essential components that allow the PLC to interact with the external environment. These devices can be either active or passive elements, depending on the function of the process and device. Active devices require an external power source to function and often include amplification or signal conditioning components. The field devices are usually physically wired into the PLC I/O modules.
Input Devices
Input devices transmit signals to the PLC, originating from various sensors and switches that monitor environmental changes. A PLC can receive various types of input signals. The two most common types are Digital Inputs (DI) and Analog Inputs (AI). A DI has two states: ON or OFF (1 or 0). Some common AI signals include 4-20mA current loops and 0-10V voltage signals.
Input devices are often used for human interaction with the process. Push buttons, like a start button, are commonly mounted on a Human Machine Interface (HMI) panel. These Switches are generally DI passive devices. Some other examples of DI’s are limit switches, toggle switches, and auxiliary contacts. DI Passive devices are usually less expensive and less complicated than active devices. Some examples of active digital input devices are proximity switches, temperature switches, level switches and pressure switches. Inputs with 24VDC are widely used in industrial automation due their safety and compatibility. However, many older systems still use 120VAC input signals.
Analog inputs can be supplied by passive or active devices as well. Analog input signals to a PLC can vary continuously over a range of voltage or current, providing detailed information about connected devices. These signals are essential for applications that require precise measurements rather than simple on/off detection. Some of the commonly used passive devices are thermocouples and resistive temperature detectors (RTDs). However, active devices are more commonly used to supply the PLC with analog inputs. Some examples of these devices include temperature sensors, pressure transducers, level sensors, and flow meters.
Output Devices
Output devices are elements that take signals from a PLC and carry out actions accordingly. They play a crucial role in implementing control commands within various industrial processes. Two Common signals from the PLC to an output device are Digital Output (DO) and Analog Output (AO).
Digital Output signals are binary (on/off) and are used to control output devices like stack lights, solenoids, relays, valves, motor starters, horns and alarms. The digital outputs are generally 24VDC or 120VAC depending on the actual device being controlled. Low voltage devices can reduce the risk of electrical shock.
Analog output signals from a PLC can continuously vary within a range, allowing for precise control of connected devices. These signals are crucial for applications that need fine adjustments rather than just on/off control. Some common devices are control valves, Variable Frequency Drives (VFDs), heaters, and hydraulic actuators.
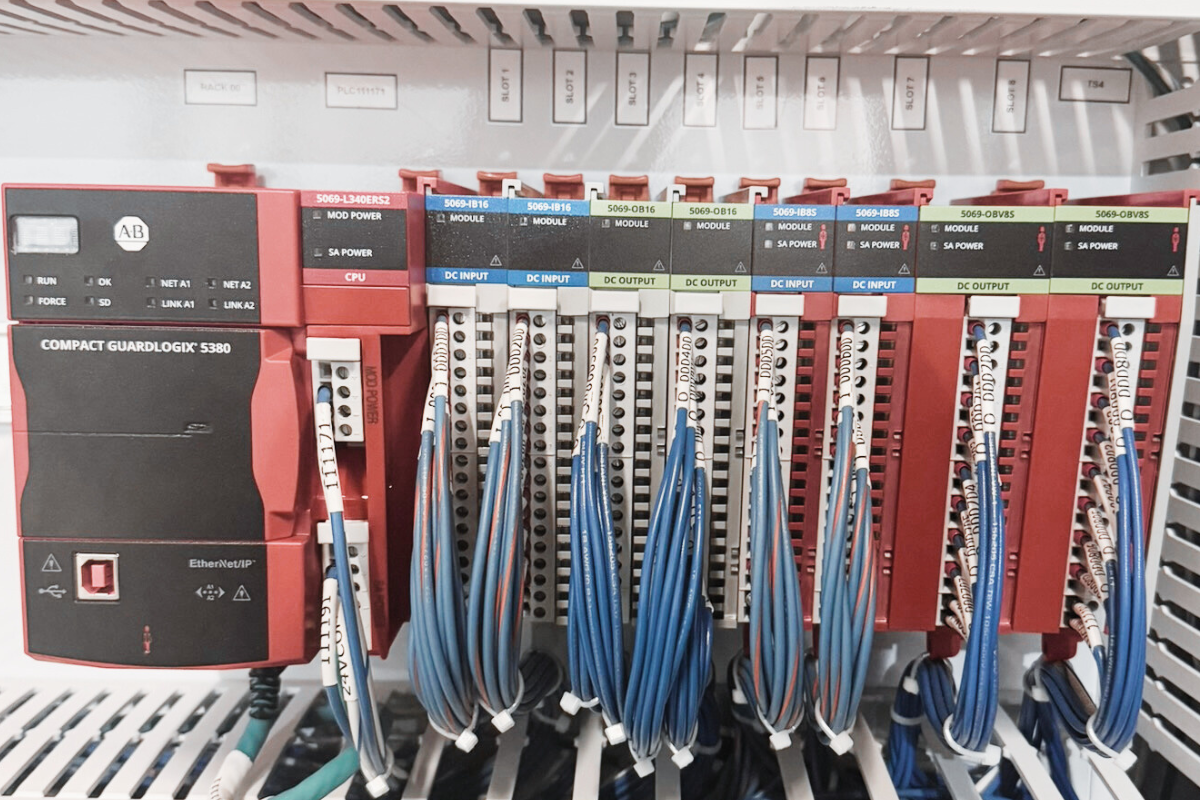
Key Hardware Components of a PLC System
Chassis:
A PLC chassis, often referred to as a rack, is the physical structure that houses the components. It is a modular system that allows for various configurations. The chassis facilitates communication between all the modules through the backplane.
Central Processing Unit (CPU):
The Central Processing Unit (CPU), or main processor, is a microprocessor-based component within a PLC. It monitors the status of field inputs, runs the control program, and issues commands to the field outputs. This sequence enables the PLC to efficiently oversee and regulate various industrial processes. For Large PLC Control Systems, Allen-Bradley and Rockwell Automation offer the ControlLogix 5580 Controllers.
I/O Modules:
There are several types of I/O modules, with the most common being Analog Output (AO), Analog Input (AI), Digital Output (DO), and Digital Input (DI). I/O modules act as the real data interface between field devices and the PLC. A PLC knows the real status of field devices and controls them with relevant I/O cards.
Human Machine Interface (HMI) with PLC:
An HMI operating station is used to provide an “operating window” to the PLC process. It is generally a separate device, like a PC and monitor, that is loaded with Human Machine Interface Software. A common Rockwell solution for an HMI is FactoryTalk View.
Programming Environment:
Rockwell Automation’s PLCs are mainly programmed using the Studio 5000® environment, a robust suite of tools crafted to simplify the development and upkeep of automation systems.
Why Use a PLC?
PLCs offer several advantages for industrial automation:
✔ Eliminate the need for rewiring when modifying control logic.
✔ Compact and scalable, allowing for customized I/O configurations.
✔ Capable of advanced control functions, such as counting, timing, and analog processing.
✔ Easy troubleshooting with built-in diagnostics.
✔ Seamless integration with HMIs and industrial networks.
✔ Cost-effective for complex automation solutions.
Why Choose Concept Systems for Your PLC Upgrades?
As a Rockwell Automation Gold System Integrator Solutions Partner, Concept Systems specializes in designing and implementing PLC control solutions that optimize efficiency, reliability, and safety. Whether you’re upgrading legacy PLCs like PLC-5s and SLCs or integrating state-of-the-art ControlLogix systems, our expert engineers ensure a seamless transition with minimal downtime.
From assessment to execution, we provide turnkey automation solutions tailored to your operational needs. If you’re looking for the right partner for your next retrofit, upgrade, or new system, Concept Systems delivers cutting-edge automation expertise to drive your business forward.
For a deeper dive into how we’ve helped companies successfully upgrade their PLC and HMI systems, check out our case study on an HMI and PLC control upgrade.
Contact us today to discuss your PLC needs and discover how we can enhance your automation strategy.