An Ignition Based Approach
Author: Ruvim Turchik, Senior Engineer
“You can have data without information, but you cannot have information without data.” —Daniel Keys Moran
Even with data collection practices in place, plant managers can be left blindfolded to bottlenecks in their manufacturing process. Manufacturing facilities generate a wealth of data every day, from machine statuses and production counts to material consumption and downtime events. This data can be overwhelming and at times useless when not handled correctly, leading to loss of production time, material, and revenue. Proper use of a plant’s data is no longer just a benefit but a necessity.
This article explains why proper data storage in a manufacturing facility matters and how the Ignition platform by Inductive Automation makes it easy and scalable. We will explore Ignition’s key data-centric components – SQL databases (including free options like MariaDB), Ignition Tag Historian, Ignition Reporting Module, Ignition Transaction Groups, and Ignition Named Queries – and see how they work together to collect, store, and leverage plant floor data.
SQL Databases:
Ignition has prebuilt SQL drives to work with standard SQL databases (like MSSQL, MariaDB, MySQL, and PostgreSQL) to store manufacturing data in an open, scalable, and cost-effective way. This allows companies to leverage well-supported technology and integrate data easily with other systems, like EMS and ERP systems. Plants can pick databases that fit their budget and infrastructure, and Ignition handles much of the database optimization automatically.
Ignition SQL Bridge Module:
The Ignition SQL Bridge Module allows for easy setup and use of transaction groups. Transaction groups allow plants to log event-based data like batch results or downtime events by defining sets of tags that are logged together on a trigger. For example, a transaction group might log all relevant production metrics when a work order is completed. These groups also allow data to be written back to PLCs, offering two-way data flow, all without needing to write code. This ensures important production data is reliably recorded in a structured way, forming the backbone of KPIs (Key Performance Indicators) like OEE (Overall Equipment Effectiveness). Take a look at the Ignition SQL Bridge Module here: https://inductiveautomation.com/ignition/modules/sql-bridge
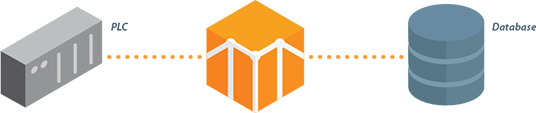
Source: Inductive Automation
Ignition Tag Historian:
The Tag Historian Module makes it simple to log time-series process data (like sensor readings) to a SQL database with just a few clicks. It automatically creates and manages database tables, compresses data, and interpolates missing points, requiring minimal setup or SQL knowledge. This enables plants to build historical records of their operations easily and cost-effectively. The historical data can then be visualized in charts and used for deeper analysis. Take a look at the Ignition Historian Module here: https://inductiveautomation.com/ignition/modules/tag-historian
Ignition Reporting Module:
The Ignition Reporting Module transforms raw data into polished, automated reports (charts, tables, PDFs) that are easy for managers to understand. You can easily set up reports to run and send out automatically, covering important metrics like production counts, downtime, material usage, and OEE. This makes it much simpler for managers to connect the dots between the data and their day-to-day decisions, helping them spot trends or problems early and take action to keep things running smoothly. Take a look at the Ignition Reporting Module here: https://inductiveautomation.com/ignition/modules/reporting

Source: Inductive Automation
Case Study and Use Cases:
The following use cases highlight two examples of valuable data that was available but not effectively utilized. Concept Systems’ engineers harnessed the power of Ignition to capture, store, and analyze this data in a clear, accessible format, enabling easier and more streamlined operations.
Material and Production Tracking
A granola manufacturing plant was struggling to keep accurate records of how much raw material was being used in each batch. The process involved mixing ingredients in set amounts, but over time, small errors and waste added up. This made it hard for plant operations to track losses and for procurement to plan ingredient orders effectively.
To solve these problems, Concept Systems set up a new system using Ignition and an MSSQL database. Ignition collected the weights of each ingredient added and the times for each batch. This created a complete record of exactly how much of each ingredient was used and how long each batch was taking.
With this system in place, the plant now had full visibility into ingredient usage. They could track every 10th pound of material that went into a batch, identify waste early, and plan purchasing with confidence. Ignition made the process simple by automating the data collection, storage, and reporting, turning raw data into valuable insights that improved both production and cost control.
Emissions Capturing and CARB Reporting
An emissions filtration company needed to track emissions data to meet CARB (California Air Resources Board) requirements. Previously, all emissions readings were manually recorded into a spreadsheet, and operations had to calculate CARB information manually.
Concept Systems implemented Ignition with a MariaDB database to automate this process. Emissions sensors were connected to Ignition, and the Tag Historian logged real-time data continuously. Using Ignition Named Queries and the Reporting Module, the system now automatically calculates and generates CARB reports, eliminating manual data entry and reducing errors.
Conclusion:
Ignition provides a powerful, flexible solution for turning raw manufacturing data into actionable insights. By working seamlessly with SQL databases, it streamlines data collection, historical logging, and automated reporting—eliminating blind spots on the plant floor and providing real-time visibility into operations. From tracking material usage to automating compliance reports, Ignition equips manufacturers to improve efficiency, reduce waste, and make well-informed decisions.
Concept Systems’ experienced engineers have supported countless manufacturers in implementing and optimizing Ignition for a wide range of applications. If you’re exploring how to unlock more value from your production data or navigate a complex integration, their expertise can help guide the way.
Ready to optimize your data workflows? Contact us to get started.